As industrial real estate has evolved over the years, automated warehouses have become increasingly important to maximize efficiency and optimize productivity. Automated warehouses are self-contained entities equipped with advanced technologies that enable goods to move quickly, accurately, and more safely than ever before. They offer a range of benefits for businesses of all sizes across multiple industries – from reducing costs and increasing speed to streamlining operations and improving customer service. In this blog post, we’ll discuss how investing in an automated warehouse can be beneficial for your business today!
Fully automating industrial properties warehouses are state-of-the-art logistics facilities that leverage advanced handling equipment and conveying systems to optimize operational performance, including efficient truck loading and unloading. These cutting-edge warehouses eliminate the need for traditional forklifts and minimize human presence within their premises.
Key Takeaways
- Automated warehouses are revolutionizing industrial real estate, offering unprecedented levels of efficiency, productivity, and accuracy, which are transforming operational dynamics and market trends in the sector.
- While automated warehouses bring substantial benefits such as cost savings and scalability, they also pose challenges including high initial investment and implementation complexities. However, ongoing advancements are continually addressing these challenges.
- The future of industrial real estate is intrinsically linked to the evolution of automated warehouses, with emerging technologies and innovations poised to further shape and define the landscape of warehousing and industrial real estate.
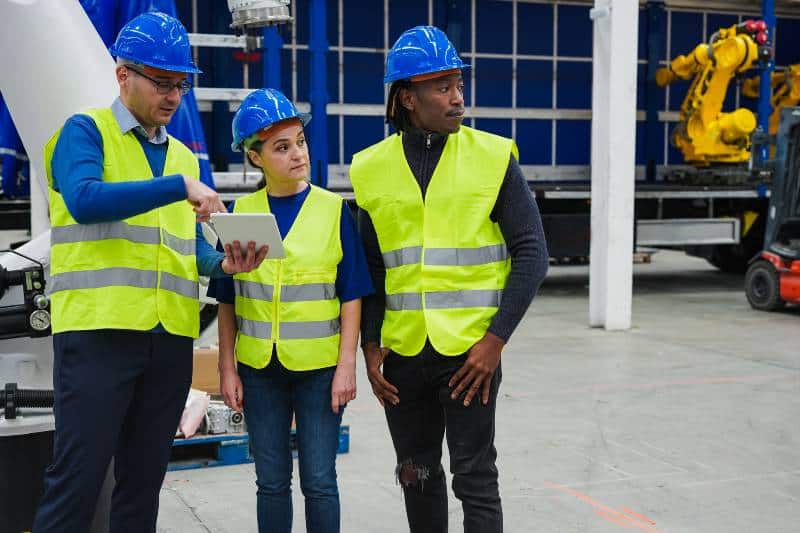
Historical Context
Evolution of Warehouses in Industrial Real Estate
The history of warehouses and their evolution in industrial real estate can be traced back to the earliest civilizations, where communal storage areas were established for the collective benefit of society. The modern concept of the warehouse, however, emerged during the industrial revolution when production, trade, and transportation changed considerably. This article aims to offer an overview of the key developments and transformations that have shaped the warehouse industry throughout history.
1. Early Warehouses
In ancient civilizations, such as those in Mesopotamia, Egypt, and Rome, warehouses were primarily used for the storage of essential food commodities like grain. Temples and palaces served as the primary repositories, ensuring better security and access control. During the medieval era, trading centers like the Hanseatic League also built large warehouses for storing goods and facilitating trade between different countries.
2. The Industrial Revolution and Modern Warehousing
The Industrial Revolution, which occurred during the 18th and 19th centuries, brought about significant changes in the nature and function of warehouses. Manufacturing processes greatly improved, leading to an increase in the production and demand for goods. Warehouses became a critical component in the supply chain process, with large storage spaces built around railways and waterways to facilitate easier transportation of goods.
3. Warehousing in the 20th Century
During the 20th century, several advancements in transportation and logistics, such as the invention of forklift trucks, shipping containers, and improved road infrastructure, contributed to the expansion of warehouse facilities. Warehouses became more specialized, and their design evolved to accommodate these new developments and cater to specific industries.
Introduction of Automation in Warehouses
Automation technology in warehouses began to gain momentum in the latter half of the 20th century, driven by technological advancements and growing demand for efficient storage and handling of goods. The introduction of automation not only streamlined processes within warehouses but also led to significant cost savings and increased productivity.
1. Early Automation
Some of the early developments in warehouse automation included the introduction of conveyor belts and other material handling equipment that assisted in the movement and storage of goods. This greatly reduced the need for manual labor, leading to higher efficiency and productivity levels.
2. Computerization and Warehouse Management Systems
The 1980s saw the introduction of warehouse management systems (WMS), which utilized computer software and databases to manage warehouse operations. This revolutionized the way warehouses functioned, allowing for improved inventory control, task management, and overall productivity.
3. Robotics and Advanced Automation Technologies
The 21st century saw the rise of robotics and other advanced automation technologies in warehouses. From automated guided vehicles (AGVs) to robotic picking and packing systems, these innovations have continued to improve the efficiency and accuracy of warehouse processes.
The evolution of warehouses in industrial properties and real estate has been a dynamic process driven by technological advancements, changing consumer demands, and global trade. The introduction of automation has significantly transformed the way warehouses operate today, offering better efficiency, cost savings, and productivity. As new innovations are introduced, warehouses will undoubtedly continue to adapt and evolve in the future.
The Rise of Automated Warehouses
Automated warehouses are revolutionizing the logistics and supply chain industry, driven by advances in technology, the need for efficient storage solutions as well as automated solutions, and increased global competition. In this article, we will discuss the current trends, the impact on the industrial real estate market, and explore case studies of successful automated warehouse implementations.
Current Trends in Automated Warehouses
Several key trends dominate the landscape of automated warehouses, as businesses are increasingly adopting advanced technology to remain competitive and enhance their operations.
- Robotics and Autonomous Vehicles: Warehouses are increasingly utilizing robots and autonomous vehicles such as automated guided vehicles (AGVs) and autonomous mobile robots (AMRs) to improve material handling, storage, picking, and transportation processes. This technology reduces human intervention, minimizing errors and increasing efficiency.
- Internet of Things (IoT) and Data Analytics: IoT devices allow automated warehouses to collect and analyze a vast amount of data in real-time. This enables better inventory management, predictive maintenance, and enhanced efficiency. Data analytics enables strategic decision-making and proactive problem-solving.
- Artificial Intelligence (AI) and Machine Learning: The application of AI and machine learning in automated warehouses enables better adaptive and predictive capabilities. These technologies improve demand forecasting, optimize warehouse layouts, and enable dynamic routing for AGVs and AMRs.
Impact on Industrial Real Estate Market
The rise of automated warehouses is significantly impacting the industrial real estate market in multiple ways:
- Increased demand for modern warehousing space: Businesses are seeking new facilities that can accommodate advanced automation features and support innovative technologies. This has spiked the demand for state-of-the-art warehousing spaces.
- Changes in space requirements: Automated warehouses often require different dimensions and layouts compared to traditional warehouses, due to the use of specialized automation equipment and the need for a more efficient workflow. This is influencing the design of new warehouses and the renovation of existing spaces.
- Location preferences: As automated warehouses enable faster, more reliable supply chains, businesses are rethinking their preferred warehouse locations. Proximity to consumers, potential for same-day delivery, and access to skilled labor are emerging as key factors driving location decisions.
Case Studies of Successful Automated Warehouse Implementations
- Amazon: As a pioneer in warehouse automation, Amazon has set the standard for the use of robotic systems in its fulfilment centers. Their Kiva robots, now called Amazon Robotics, have streamlined the picking and packing processes, significantly increasing efficiency, speed, and warehouse capacity.
- Ocado: This UK-based online grocery retailer has implemented an advanced warehousing system that uses thousands of collaborative robots, working on a 3D grid known as “The Hive.” The robots pick and pack customer orders, dramatically reducing order processing time and labor costs.
- XPO Logistics: XPO Logistics utilizes robotic lift machines, robotic palletizing machines, and AGVs in its warehouses. Their investment in automation has enabled them to increase efficiency, improve order accuracy, and attract more customers.
The rise of automated warehouses is transforming not only the logistics and supply chain industry but also the industrial real estate market. As businesses continue to invest in modern technological solutions and innovative warehouse designs, automated warehouses will continue to gain momentum and shape the future of industrial real estate and warehousing operations.
Benefits of Automated Warehouses
Automated warehouses, through the use of cutting-edge technology, are fundamentally reshaping the way goods are stored and operations are conducted in the logistics and supply supply chain industry. The adoption of autonomous systems in warehouse operations comes with an array of significant benefits, ranging from increased efficiency and cost savings to improved accuracy and scalability.
Efficiency and Productivity
One of the primary benefits derived from warehouse automation is a significant boost in efficiency and productivity. Automated systems, like conveyors, automated guided vehicles (AGVs), and robotic picking, can handle repetitive tasks faster and more efficiently than human labor. This results in shorter lead times, increased throughput, and greater capacity to handle peak periods.
Cost Savings
Warehouse automation can bring about substantial cost savings. By reducing the dependency on manual labor, automated systems can decrease labor-related costs. Furthermore, improved speed and efficiency result in shorter turnaround times, reducing inventory holding costs. Automation also reduces the risk of workplace injury, which can lead to potential savings in insurance costs and absenteeism.
Accuracy and Reliability
Automated warehouses significantly improve accuracy in operations, thereby mitigating the risk of errors associated with manual interventions. Such systems demonstrate high consistency in picking, ensuring fewer picking errors. Other functions like sortation, packing, and shipping also benefit from increased accuracy, expect existing users, customer satisfaction and fewer returns.
Scalability
Automated warehouses offer excellent scalability, which serves as a significant advantage for businesses that face peak demand periods. During high-volume periods, automated systems can be ramped up to handle increased loads. Additionally, as businesses grow, automation systems can be expanded or upgraded facilitating scalable and sustainable growth.
In conclusion, the benefits of automated warehouses are manifold, and businesses stand to gain tremendously from their adoption. Increased efficiency and productivity, cost savings, improved accuracy and reliability, and scalable solutions contribute to a robust and flexible supply chain and logistics operation that can meet the demands of an ever-evolving market scenario.
Challenges and Solutions of Automated Warehouses
While automated warehouses bring about numerous benefits, implementing automation in the warehouse environment also comes with its share of challenges. One of the key challenges businesses face is the initial investment and execution challenges. This section outlines these hurdles along with potential solutions.
Initial Investment
Challenge
The primary challenge for many businesses when considering automated warehousing is the significant initial capital investment. Implementation of automation systems can be high cost, incorporating expenses for equipment, software, infrastructure modifications, and training of personnel.
Solution
While the initial costs of automation can be high, organizations must view automation as a long-term investment delivering substantial ROI in the form of operational efficiency, productivity improvements, reduced labor costs, and minimization of error-related expenses. Adopting phased implementation, starting with automating critical processes in smaller scales before extensive deployment, can help manage costs while reaping benefits.
Implementation Challenges
Challenge
Implementation of warehouse automation is a complex process that involves careful planning, design, coordination, and execution. Businesses have to handle challenges related to technology selection, process re-engineering, system integration, and workforce training.
Solution
Proper planning and phased implementation can mitigate these challenges. Engaging with experienced automation vendors, investment in staff training, and conducting pilot projects can assist in smooth transition. After successful pilot implementation, organizations can gradually roll out the automation in different warehouse areas.
While the shift towards automated warehouses comes with initial investment and implementation challenges, strategic planning and phased implementation can help overcome these hurdles, paving the way for enhanced operational efficiency and cost-effectiveness in the long run.
Future of Automated Warehouses
The continued evolution of automation technologies and their successful integration into warehouse operations suggests a future where automation becomes the baseline setting for warehouse operations. This article will provide a glimpse into the potential future of automated warehouses, highlighting predictions, future trends, and emerging technologies that will shape the automated warehouse landscape.
Predictions and Trends
Increasing Adoption of Automation
Automation will increasingly become the standard for warehouses. More businesses will recognize the benefits of automation in terms of efficiency, cost savings, accuracy, and scalability, leading to increased adoption across industries. Smaller businesses will also gradually adopt automation, driven by the availability of more affordable and flexible semi automation solutions.
Integration of Warehouse Management Systems (WMS) and Robotics
The future holds a more seamless integration between WMS and robotics. With advancements in artificial intelligence and machine learning, warehouse robots will work closely with WMS, enabling more responsive and adaptive warehouse operations.
The Rise of Data-Driven Warehousing
Data-driven decision-making will play an increasingly significant role in warehouse operations. Using advanced analytics, warehouses will be able to make informed predictions, optimize inventory levels, improve warehouse layouts, and handle peak offerings better.
Emerging Technologies in Warehouse Automation
Robotics as a Service (RaaS)
In an effort to mitigate implementation risks for warehouse operators, certain investors and developers are shifting towards a model known as Robotics as a Service (RaaS). Under this model, warehouse operators have the opportunity to lease robotic devices like Automated Guided Vehicles (AGVs) and Autonomous Mobile Robots (AMRs) rather than outright purchasing them.
According to Guevarra, “RaaS serves to alleviate the initial upfront expenses, thereby offering flexibility.” The introduction of this model is instrumental in closing the mechanization and automation gap for numerous small to medium-sized enterprises, along with third-party logistics (3PL) providers seeking more adaptable semi-automation solutions and semi automation technologies.
The trend towards RaaS is quickly gaining momentum as it effectively eliminates the barriers to entry typically associated with automation, making it easier for businesses to harness the efficiency and productivity gains offered by robotic automation, without a substantial upfront capital investment.
Use of Drones
Warehouses of the future may increasingly use drones for tasks such as inventory checks or small item picking. Drones, with their capability to navigate vertically as well as horizontally, can provide a speed and efficiency advantage for certain warehouse tasks.
Advanced Machine Learning & AI
Machine learning and AI will continue to advance and play an increasing role in warehouse automation. These technologies will enable intelligent routing, predictive analytics, demand forecasting, and more automated decision-making processes.
The future of automated warehouses looks promising with the rapidly progressing technology and the increasing understanding of automation benefits. Businesses that keep pace with these advancements will be well-positioned to benefit from increased operational efficiency and competitive advantage.
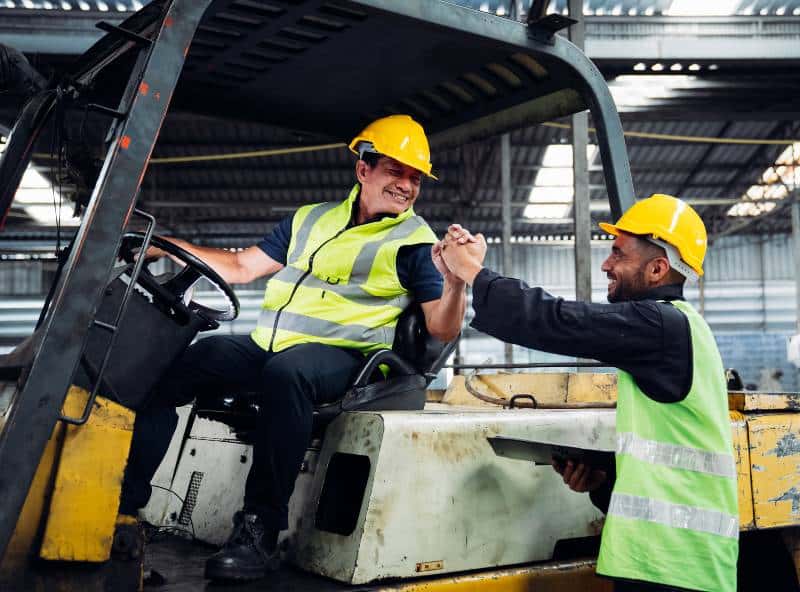
Automated Warehouses in Industrial Real Estate FAQs
What is an automated warehouse?
An automated warehouse is a type of warehouse that uses technology, such as robotics, artificial intelligence, and advanced software systems, to automate various tasks and processes within the warehouse. This allows for increased efficiency, accuracy, and productivity in operations.
What is the function of an automated warehouse?
The primary function of an automated warehouse is to improve efficiency and productivity in warehousing operations. This is achieved through the use of technology that automates various tasks, such as inventory management, order fulfillment, and material handling. Automation also helps reduce errors, increase speed, and decrease labor costs.
What are the benefits of the automated warehouse?
The benefits of automated warehouses include increased operational efficiency, improved accuracy and productivity, reduced labor costs, and better management of peak demand periods. Automation also helps businesses stay competitive in a rapidly evolving market.
How automated warehouse can increase warehouse efficiency?
Automated warehouses can increase efficiency by reducing the time and effort needed to perform various tasks, such as inventory management and order fulfillment. Automation also helps minimize errors and delays in operations, enabling more streamlined warehouse processes.
What is the impact of automation in warehouse management?
The primary way automation adds value is by increasing efficiency. Automating specific processes within the warehouse allows time and work to be reallocated elsewhere. Instead of someone walking a material from one station to another, a conveyor belt can take the material automatically to the next workstation.
Conclusion
The rise of automated warehouses has had an undeniable impact on commercial real estate. Automated warehouses have unlocked greater efficiency, scalability, and accuracy to elevate operations and markets, while lowering costs.
However, complexity and initial investment is a barrier that still requires further technological thrusts. As emerging technologies continue to refine solutions for these limitations, industrial real estate will only become further integrated with automated warehousing towards unlocking greater potential.
If you are an investor or individual looking to make the right investments as automation rises in retail and warehousing – Call or schedule a free consultation for more retirement tips like reverse mortgages- this is your opportunity!
With all the benefits automated warehouses have to offer, now is your time to capitalize on the advances of modern technologies to develop more profitable industrial space investments.