The global warehousing market reached a staggering $1.01 trillion in 2023 and is projected to grow at an impressive 8.1% from 2024 to 2030. Standing at the crossroads of your business journey, you face a pivotal choice. On one path, a towering warehouse reaches skyward, promising vast storage potential. On the other, a more modest facility offers familiar efficiency. In today’s competitive landscape, where every square foot counts, understanding the distinction between high-bay and low-bay warehouses isn’t just helpful – it’s crucial for optimizing your operations and ensuring future success. Let’s explore how each option could transform your storage capabilities and set your business apart.
Key Takeaways
- High-bay warehouses (20-45+ feet) maximize vertical storage for large operations, while low-bay facilities (10-20 feet) suit smaller-scale needs
- Lighting solutions and automation capabilities differ significantly between the two types, impacting operational efficiency
- The choice between high-bay and low-bay depends on factors like budget, storage needs, and future scalability requirements
Expert Insights, Exceptional Outcomes
Transform challenges into opportunities with Tolj Commercial’s consultation services. Our tailored advice empowers you to make decisions that drive long-term success.
Expert Insights, Exceptional Outcomes
Transform challenges into opportunities with Tolj Commercial’s consultation services. Our tailored advice empowers you to make decisions that drive long-term success.
Understanding the Basics: Height Matters
Let’s start with the fundamental difference between these warehouse types. Think of it like choosing between a high-rise apartment and a townhouse – each serves its purpose, but they cater to different needs.
High-Bay Specifications
High-bay warehouses are the skyscrapers of the storage world. With ceiling heights soaring from 20 to 45+ feet, these facilities are perfect for businesses that think vertically. I recently helped a client in the e-commerce sector maximize their storage capacity by going vertical – they effectively tripled their storage capacity without increasing their footprint!
Key advantages include high and low bay lighting options.
- Maximum space utilization
- Ideal for automated storage systems, especially in high and low bay scenarios.
- Perfect for large inventory volumes
- Efficient use of land area
Low-Bay Characteristics
On the flip side, low-bay warehouses High and low bay warehouses typically range from 10 to 20 feet in height. These are your bread-and-butter facilities, perfect for smaller operations or businesses with frequent inventory turnover.
Lighting: Illuminating the Differences
Let’s shed some light on one of the most crucial aspects of warehouse design.
High-Bay Lighting Solutions
High-bay lighting requires careful consideration. We’re talking about illuminating spaces from great heights, which presents unique challenges:
Aspect | Requirement |
---|---|
Lumen Output | 15,000+ lumens |
Coverage Area | Wide beam angle |
Energy Efficiency | LED preferred |
Smart Controls | Motion sensors & automation |
Low-Bay Lighting Considerations
When it comes to low-bay lighting In a high or low-bay environment, the approach is more straightforward but requires careful attention to detail. These facilities typically demand lower lumen requirements, ranging from 8,000 to 15,000 lumens, which provides optimal illumination for their shorter ceiling heights.
The lighting design benefits from broader light distribution patterns, creating uniform coverage across the workspace. What makes low-bay lighting particularly efficient is the flexibility in fixture placement – the lower mounting heights allow for more strategic positioning of light sources to eliminate shadows and dark spots.
Additionally, maintenance becomes significantly more manageable, as fixtures are easily accessible for repairs and replacements without requiring specialized equipment.
Modern Operations and Automation
In today’s fast-paced world, warehouse operations have evolved far beyond simple storage solutions. The integration of technology and automation has revolutionized how we approach warehouse management and efficiency, particularly in high and low-bay settings.
High-Bay Operations
High-bay facilities excel in leveraging advanced technology for maximum efficiency. At their core, these warehouses utilize sophisticated automated storage systems that can navigate the full vertical height of the space. The implementation of cutting-edge picking technologies allows for precise inventory management at all levels. Vertical lift modules serve as the backbone of these operations, enabling rapid access to items stored at any height.
These systems work in conjunction with complex racking arrangements that maximize every cubic foot of available space while maintaining organized, efficient storage solutions.
Low-Bay Operations
Low-bay operations offer a more hands-on and adaptable approach to warehouse management. The reduced ceiling height creates an environment where inventory is readily accessible, allowing for more direct interaction with stored items.
These facilities typically employ simpler material handling equipment, reducing both training requirements and maintenance costs for high and low-bay lighting solutions. The layout of low-bay warehouses provides greater flexibility for reorganization and adaptation to changing business needs.
This adaptability extends to storage arrangements, which can be easily modified to accommodate seasonal changes or shifting inventory patterns.
The Future is Smart: Technology Integration
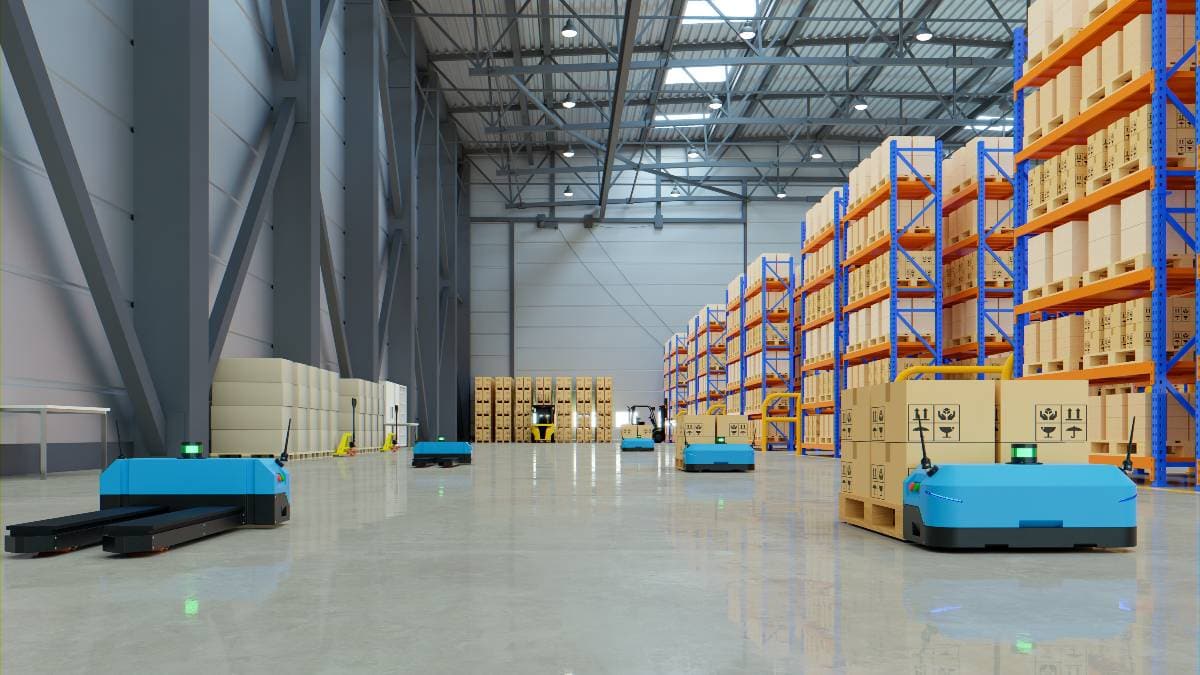
The landscape of warehouse management is being transformed by smart technology. Through my experience with a medium-sized distributor last year, I witnessed firsthand how smart warehouse solutions can revolutionize operations. The implementation of integrated technology systems yielded remarkable improvements in efficiency and accuracy.
High-Bay Automation Solutions
High-bay facilities are at the forefront of automation innovation. The implementation of Automated Storage and Retrieval Systems (AS/RS) has revolutionized how these warehouses operate. Sophisticated robotic picking solutions work seamlessly with AI-powered inventory management systems to optimize storage and retrieval operations. Vertical lift modules further enhance efficiency by maximizing the use of vertical space while maintaining quick access to inventory.
Low-Bay Automation Integration
Low-bay facilities have embraced automation in their own unique way. Semi-automated picking systems provide an excellent balance between efficiency and flexibility. Smart inventory tracking systems ensure accurate stock management without the complexity of full automation.
These warehouses benefit from flexible automation options that can be scaled according to needs, whether in high or low bay configurations. The integration of IoT sensors enables real-time monitoring and optimization of warehouse operations, ensuring maximum efficiency within space constraints.
Making the Financial Case
As a commercial real estate professional, I always emphasize the importance of looking at the complete financial picture.
Cost Considerations Table
Factor | High-Bay | Low-Bay |
---|---|---|
Initial Construction | Higher | Lower |
Operating Costs | Variable | Lower |
Energy Efficiency | Complex | Simpler |
Automation Investment | Substantial | Moderate |
Maintenance | More Complex | Straightforward |
Environmental Impact and Sustainability
In today’s market, environmental sustainability and Sustainable Property Management has become a crucial factor in warehouse selection and design. Through my experience working with various clients, I’ve observed a significant shift in how businesses approach their environmental impact when choosing between high-bay and low-bay facilities.
High-bay warehouses offer unique advantages in terms of sustainability. Their vertical design naturally leads to a smaller physical footprint, which means less land usage and reduced environmental impact. This vertical optimization also translates to more efficient climate control systems, as the concentrated space allows for more precise temperature and humidity management.
Many of my clients have successfully implemented advanced energy management systems in their high-bay facilities, resulting in substantial reductions in their carbon footprint.
Low-bay warehouses, while different in their approach to sustainability, offer their own set of environmental benefits. Their lower height profile makes them ideal candidates for natural lighting solutions, which can significantly reduce energy consumption during daylight hours.
The simpler HVAC requirements of low-bay facilities often result in lower overall energy usage, and their roof structures are typically better suited for solar panel installation.
Real-World Success Stories
The Woodbridge Group Manufacturing Facility
The Woodbridge Group upgraded to Essentials Series 4.0 LED high bays, achieving a 73% reduction in energy consumption. This upgrade not only met their two-year payback requirement but also improved light levels, enhancing visibility and safety for over 300 employees. The estimated annual savings on utility bills reached $83,890. More details can be found in the Linmore LED case study.
Automotive Parts Distribution Center in Michigan
This facility implemented Hubbell’s MGHB LED High Bay fixtures with integrated controls, resulting in a 72% reduction in lighting energy costs. The improved lighting levels significantly enhanced worker productivity, and the facility manager reported a return on investment within 18 months due to energy savings and reduced maintenance costs. More information is available at Warehouse Whisper.
Cold Storage Facility in Texas
A cold storage facility replaced traditional lighting with Dialight’s Vigilant High Bay LED luminaires, achieving a 70% reduction in energy consumption. The improved visibility in extreme cold conditions led to increased worker productivity and reduced accidents, supported by a robust 10-year warranty on the fixtures. Details can be found at Clear Sky Distributors.
General Warehouse Upgrade
A client upgraded their warehouse with 150W Diamond-DS LED High Bays, moving from aging 400W HID fixtures. Post-installation, illumination levels increased from an average of 72lx to 311lx, resulting in over a 60% reduction in energy costs and minimal maintenance needs for the next 50,000 hours. This project showcased significant improvements in light quality and operational efficiency. More information is available at Clear Sky Distributors.
Low-Bay Warehouse Considerations
While specific low-bay warehouse case studies were not highlighted, it is important to note that low-bay lighting solutions are typically used for spaces with lower ceiling heights (under 20 feet). These solutions often focus on cost-effectiveness and energy efficiency while providing adequate illumination for operations.
These case studies illustrate the effectiveness of high-bay lighting solutions in various warehouse settings, emphasizing energy savings, improved productivity, and enhanced safety for workers.
Looking to the Future
The warehouse industry is undergoing rapid transformation, driven by technological advances and changing market demands. Based on my extensive experience in commercial real estate, I’ve identified several key trends that are shaping the future of both high-bay and low-bay warehouses.
IoT integration is becoming increasingly prevalent in both warehouse types, enabling real-time monitoring and predictive maintenance. Smart sensors and connected systems are revolutionizing how we approach warehouse management, regardless of ceiling height. The adoption of sustainable building materials is also gaining momentum, with new technologies enabling better insulation and energy efficiency.
AI-powered operations are another game-changer, particularly in high-bay facilities where complex automation systems can be fully leveraged. However, we’re also seeing innovative applications of AI in low-bay warehouses, particularly in inventory management and order fulfillment optimization.
Perhaps most intriguingly, we’re witnessing the emergence of hybrid storage solutions that combine elements of both high-bay and low-bay designs. These innovative approaches allow businesses to maximize the benefits of both configurations while minimizing their respective drawbacks.
Making Your Decision
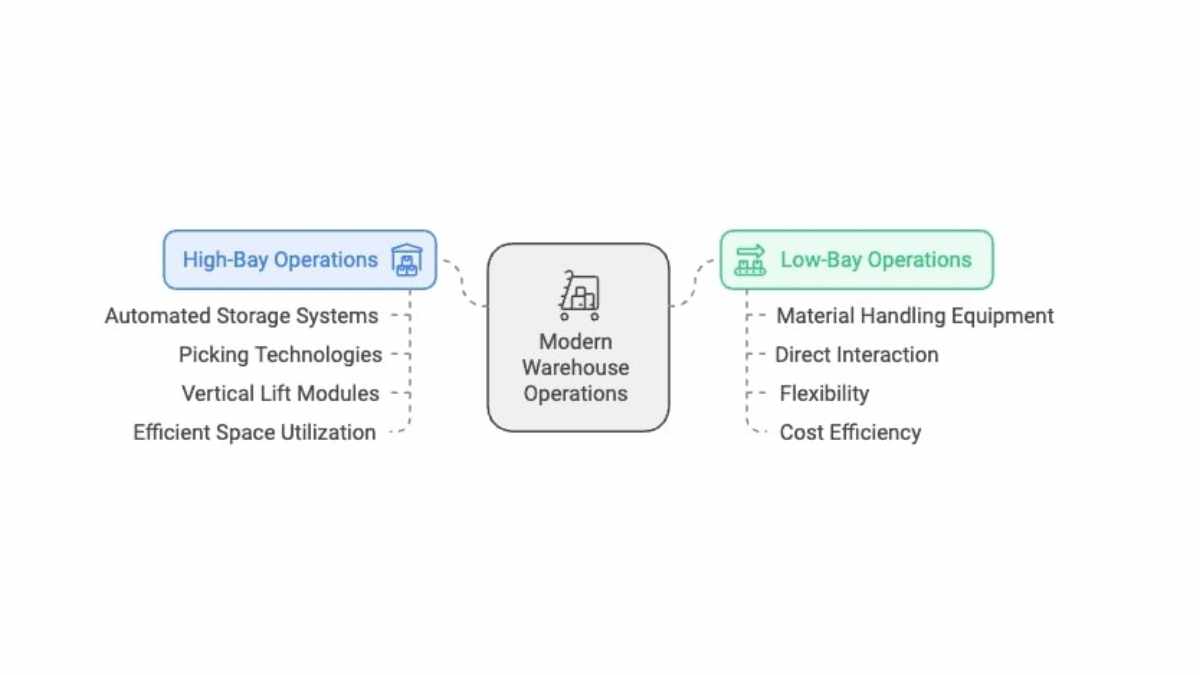
Choosing between a high-bay and low-bay warehouse requires careful consideration of multiple factors, including bay vs low-bay light efficiency. Through my 18 years in commercial real estate, I’ve developed a comprehensive approach to helping clients make this crucial decision.
Current needs must be balanced against future growth projections. I always encourage clients to think about where their business will be in 5-10 years, not just their immediate requirements.
Budget constraints obviously play a crucial role, but it’s important to consider both initial investments and long-term operational costs. Location and land costs can significantly impact the decision, particularly in urban areas where vertical storage might be more cost-effective.
Expert Insights, Exceptional Outcomes
Transform challenges into opportunities with Tolj Commercial’s consultation services. Our tailored advice empowers you to make decisions that drive long-term success.
Expert Insights, Exceptional Outcomes
Transform challenges into opportunities with Tolj Commercial’s consultation services. Our tailored advice empowers you to make decisions that drive long-term success.
FAQs
What is the main difference between high-bay and low-bay warehouses?
How do I choose the right bay lighting for my warehouse?
What types of light fixtures are used in high bay vs low bay applications?
Can I use LED lights in both high bay and low bay settings?
Why should I consult a CRE expert before selecting a warehouse type?
How can a CRE expert help optimize my warehouse investment?
Conclusion
The choice between high-bay and low-bay warehouses isn’t just about height – it’s about your business’s future. Think of it as choosing between a custom-tailored suit and a versatile blazer; both have their place, but the right choice depends on your unique style and needs. Whether you’re reaching for the sky with a high-bay facility or maximizing efficiency in a low-bay space, success lies in aligning your choice with your operational vision. Ready to take the next step? Let’s transform your warehouse dreams into reality. Schedule a consultation with me!