Tired of watching your industrial property insulation costs soar? You’re not alone. After helping hundreds of property owners tackle their insulation challenges over 18 years, I’ve seen energy bills drop by up to 35% with the right approach. Whether you’re managing a warehouse, manufacturing facility, or commercial space, this guide will show you exactly how smart insulation solutions can transform your energy efficiency. Let’s turn those costly energy leaks into lasting savings.
Key Takeaways
- Implementing proper insulation efficiency measures can reduce energy costs by 13-35% in commercial buildings
- Strategic insulation improvements can save over 700 therms of natural gas annually in just 25% of commercial buildings
- Modern insulation solutions with AI integration can enhance operational efficiency by up to 84%
Expert Insights, Exceptional Outcomes
Transform challenges into opportunities with Tolj Commercial’s consultation services. Our tailored advice empowers you to make decisions that drive long-term success.
Understanding the Fundamentals
When I first started in commercial real estate, I noticed that many property owners overlooked the basics of industrial insulation. It’s not just about stuffing material in walls – it’s about creating an intelligent system that works for your specific needs.
Temperature Management
The primary role of industrial insulation is precise temperature control. Think of your building as a giant thermos – you want to keep hot things hot and cold things cold. In manufacturing facilities, this might mean containing process heat. For cold storage, it’s about maintaining those crucial low temperatures without skyrocketing energy bills.
Energy Flow Control
Here’s something that still amazes me after 18 years: proper insulation can slash energy costs by up to 35%. It’s all about managing heat flow. When we talk about thermal resistance and R-values, we’re really discussing how effectively your insulation product creates a barrier against unwanted heat transfer.
Sound Control Benefits
Let’s talk about an often-overlooked benefit: noise reduction. In industrial settings, sound control isn’t just about comfort – it’s about compliance and worker productivity. Good insulation can significantly reduce both external noise pollution and internal sound transmission between spaces.
Moisture Management
Moisture is the silent destroyer in industrial properties. Without proper vapor barriers and insulation, condensation can lead to mold growth, material degradation, and structural issues. I’ve seen moisture problems turn into costly renovations that could have been prevented with proper insulation strategies.
Performance Metrics
When evaluating insulation performance, we focus on two critical measurements. First, there’s the R-value – think of it as your insulation’s effectiveness score. The higher the R-value, the better it resists heat flow. Then there’s thermal conductivity – how readily heat moves through the material. Together, these metrics help us choose the right solutions for your specific needs.
Application Considerations
Different industrial spaces demand different approaches. A data center requires precise temperature control to protect sensitive equipment, while a manufacturing facility might need high-temperature insulation for process equipment. Understanding these specific needs is crucial for selecting the right insulation types and strategies.
Steps To Improving Insulation For Your Commercial Building
Step 1: Assess Your Current Insulation Status
Starting with a comprehensive evaluation is crucial. A professional energy audit will include thermal imaging to detect heat loss areas and air leaks throughout your building. During my assessments, I always ensure we thoroughly examine R-values and moisture levels, as these are key indicators of insulation performance.
Most commercial building insulations have common problem areas that require special attention. In my experience, the roof and ceiling spaces often show significant heat loss. Wall cavities, particularly around windows and doors, frequently need addressing. The foundation, pipe systems, and HVAC ductwork are also critical areas where insulation efficiency can be improved.
Step 2: Choose the Right Insulation Materials
Material selection is vital for achieving optimal efficiency. Traditional options like fiberglass remain popular for walls and ceilings due to their cost-effectiveness and proven performance. Mineral wool excels in areas requiring high-temperature resistance, making it ideal for industrial applications. Cellulose, made from recycled materials, works exceptionally well for retrofitting existing spaces.
Modern solutions have expanded our options significantly. Spray foam applications provide superior air sealing and can reach difficult spaces. Radiant barriers effectively reduce heat gain, especially in roof spaces. Smart insulation systems integrated with building management technology offer new levels of control and efficiency.
Step 3: Implement Strategic Improvements
Implementation requires careful planning and execution. Begin by sealing air leaks, as these quick fixes often provide immediate returns. Next, focus on roof insulation, as heat naturally rises and this area typically shows the highest heat loss. Wall insulation and foundation areas should follow, with mechanical systems being addressed throughout the process.
Working with certified contractors is essential for proper installation. They understand building codes and can plan the work to minimize business disruption. Weather conditions during installation can significantly impact effectiveness, so timing is crucial.
Step 4: Integrate Smart Technology
Modern commercial insulation efficiency goes beyond traditional materials. Real-time monitoring systems can track performance and identify issues before they become problems. Temperature zone control allows for precise management of different areas based on specific needs. Energy usage optimization helps maintain peak efficiency throughout your building.
Step 5: Monitor and Maintain
Regular maintenance ensures long-term performance. Monthly visual inspections can catch early signs of degradation or damage. Quarterly performance checks help verify that your insulation continues to meet efficiency standards. Document all maintenance activities and track performance metrics to maintain optimal efficiency.
Step 6: Measure ROI
Understanding your return on investment requires tracking specific metrics. Monitor your energy costs before and after improvements. Track temperature stability throughout your building and note any changes in comfort levels reported by occupants or staff. Equipment maintenance costs often decrease with proper insulation, so track these expenses as well.
The industrial insulation market continues to grow as more property owners recognize its importance in reducing operating costs and improving building performance. By following these steps and maintaining a proactive approach to insulation management, you can achieve significant improvements in your building’s efficiency.
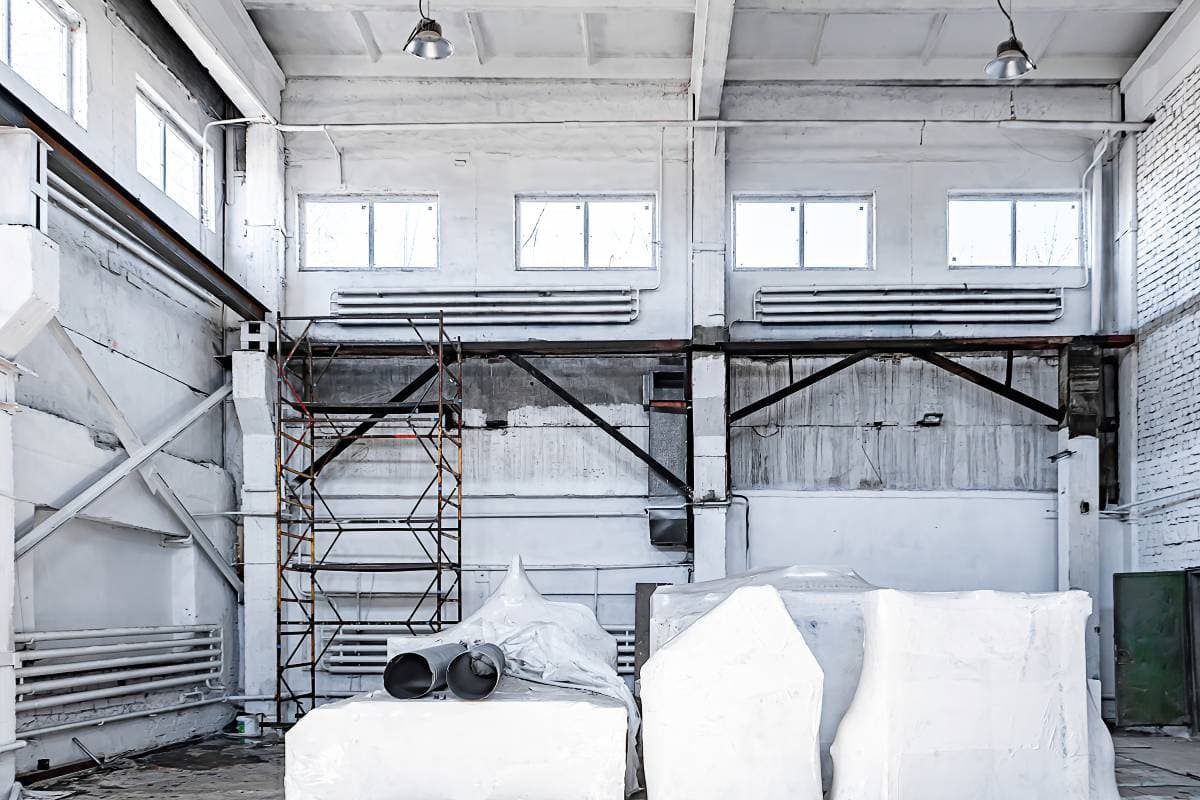
Looking to the Future
The landscape of industrial property insulation is rapidly evolving, and as someone who’s been in commercial real estate for nearly two decades, I’m excited about the innovations I’m seeing. Here is what’s currently shaping the future of insulation efficiency.
Bio-based Materials
The shift toward sustainable solutions has brought bio-based insulation materials to the forefront. These materials, derived from renewable sources like hemp, cotton, and mushroom-based compounds, are showing promising thermal performance while reducing environmental impact.
Smart Building Integration
The integration of insulation with building management systems is becoming increasingly sophisticated. Modern buildings now feature sensor networks that monitor temperature, humidity, and energy performance in real time. This allows for dynamic adjustments to maintain optimal conditions while minimizing energy consumption. The ability to detect and respond to changing conditions automatically represents a significant leap forward in building efficiency.
Improved Manufacturing Techniques
Advancements in manufacturing processes are leading to insulation materials with enhanced performance characteristics. We’re seeing the development of thinner materials that provide better insulation values, reducing the space needed while improving efficiency. These innovations are particularly valuable in retrofit projects where space is at a premium.
Sustainability Focus
The push toward net-zero buildings is driving innovation in insulation technology. New materials and installation methods are being developed with their full lifecycle impact in mind. This includes not just their insulating properties, but also their recyclability, embodied carbon, and long-term environmental impact.
Regulatory Influence
Building codes and energy efficiency standards continue to evolve, pushing the industry toward more effective solutions. I’m seeing an increased emphasis on whole-building performance rather than just meeting minimum R-value requirements. This holistic approach is leading to better integration of insulation with other building systems.
Monitoring and Performance Verification
The future of insulation includes more sophisticated ways to verify and maintain performance over time. Advanced imaging technologies and continuous monitoring systems are making it easier to identify and address efficiency losses before they become significant problems. This proactive approach helps maintain optimal performance throughout the building’s lifecycle.
Research and Development
Ongoing research in material science and building physics is opening new possibilities for insulation technology. From phase-change materials that actively manage heat flow to aerogel-based products that provide superior insulation with minimal thickness, the pipeline of innovations continues to grow. These developments promise to make buildings more efficient and comfortable while reducing their environmental impact.
Expert Insights, Exceptional Outcomes
Transform challenges into opportunities with Tolj Commercial’s consultation services. Our tailored advice empowers you to make decisions that drive long-term success.
FAQs
What’s the first step in improving insulation efficiency?
How much can I expect to save with improved insulation?
Should I upgrade all insulation at once?
How do smart technologies enhance insulation efficiency?
What’s the most important maintenance step?
Conclusion
Ready to take your property’s efficiency to the next level? These steps provide a solid framework for improvement, but every property is unique. I’d love to help you develop a customized strategy that maximizes your insulation efficiency. Schedule a consultation with me and let’s discuss how we can optimize your property’s performance while minimizing your energy costs.