As someone who’s spent nearly two decades in commercial real estate, I’ve seen countless industrial property owners struggle with temperature control. Let me tell you, implementing temperature zoning in industrial properties isn’t just a fancy upgrade – it’s becoming essential for modern industrial facilities. The impact on operational efficiency and cost management can be truly transformative. In today’s competitive market, proper climate control can make the difference between thriving and just surviving.
Key Takeaways
- Temperature zoning can reduce energy costs by up to 30% in industrial properties
- Proper zoning implementation creates optimal conditions for diverse storage requirements
- Modern building automation systems enhance control and monitoring capabilities
Expert Insights, Exceptional Outcomes
Transform challenges into opportunities with Tolj Commercial’s consultation services. Our tailored advice empowers you to make decisions that drive long-term success.
Expert Insights, Exceptional Outcomes
Transform challenges into opportunities with Tolj Commercial’s consultation services. Our tailored advice empowers you to make decisions that drive long-term success.
Understanding Temperature Zoning Fundamentals
Core Components
Think of temperature zoning as having multiple thermostats in your home, but on an industrial scale. At its core, a zoning system consists of sophisticated zone dampers, independent thermostats, and a central control panel that works in harmony with your existing HVAC infrastructure.
Types of Temperature Zones
The beauty of modern climate-controlled environments lies in their ability to maintain different temperatures across various spaces. Whether you’re dealing with ambient storage, cold storage, or specialized environmental zones, each area can be precisely controlled to meet specific requirements.
Business Case Analysis
Return on Investment
The financial benefits of implementing temperature control systems are compelling. Based on my experience working with numerous clients, most facilities see a return on investment within 2-3 years through reduced energy consumption and improved operational efficiency.
Investment Factor | Typical Return |
---|---|
Energy Savings | 20-30% |
Maintenance Reduction | 15-25% |
Product Loss Prevention | 10-20% |
Risk Assessment
When we talk about risk assessment, it’s crucial to consider both the implementation challenges and ongoing operational considerations. A well-planned zoning system includes redundancies and failsafes to ensure business continuity.
Implementation Strategies
Assessment Process
Success in temperature zoning implementation starts with thorough assessment and planning. During my years helping clients transform their industrial spaces, I’ve learned that understanding the facility’s unique needs is crucial. Your building automation system should be tailored to your specific operations, not the other way around.
System Design
A well-designed zoning system considers current needs while planning for future expansion. This might mean implementing more sophisticated control systems or preparing for additional zones as your business grows. The key is creating a flexible foundation that can adapt to changing needs.
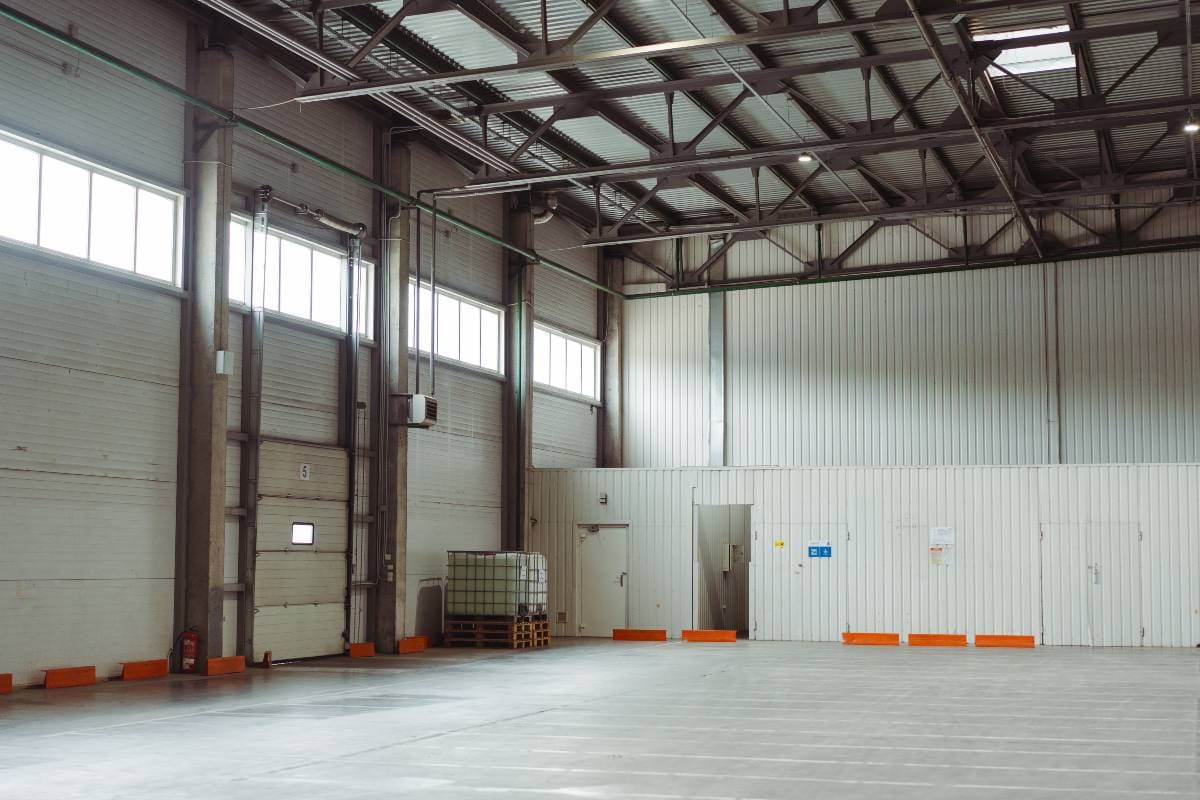
Regulatory Compliance and Standards
Industry Requirements
In today’s complex regulatory environment, compliance isn’t just about checking boxes. Different industries face unique challenges in maintaining proper environmental conditions.
Industry Type | Temperature Requirements | Compliance Standards |
---|---|---|
Food Storage | 34-39°F | FDA, HACCP |
Pharmaceuticals | 68-77°F | GMP, cGMP |
Chemical Storage | Varies | OSHA, EPA |
Environmental Standards
Modern temperature control systems must meet increasingly stringent environmental regulations while maintaining optimal operational efficiency.
Benefits and Applications
Operational Advantages
The advantages of proper temperature zoning extend far beyond basic climate control. Through strategic implementation, facilities can achieve:
Cost Reduction
I’ve witnessed firsthand how these systems transform industrial operations. One of my clients, a large distribution center, reduced their energy costs by 35% within the first year of implementation.
Case Studies and Success Stories
Large Facility Implementation
A 200,000-square-foot multi-use industrial facility case study revealed:
Metric | Improvement |
---|---|
Energy Costs | -32% |
Temperature Consistency | +85% |
Tenant Satisfaction | +40% |
Success Metrics
The transformation wasn’t just about numbers – it revolutionized their entire operation.
Best Practices and Optimization
Installation Guidelines
The success of your temperature control system depends heavily on proper implementation and maintenance. Based on my experience, the key is finding the right balance between automation and human oversight.
Maintenance Protocols
Your facility managers should understand the system while letting the building automation handle day-to-day adjustments.
System Optimization
Regular monitoring and adjustment ensure peak performance and efficiency.
Future Trends and Technologies
Emerging Technologies
The future of industrial temperature zoning is incredibly exciting. We’re seeing the emergence of AI-driven systems that can predict and adjust to changing conditions before they become issues.
Smart Integration
Smart building integration is becoming the norm, not the exception, with systems that communicate and adapt in real time.
Implementation Checklist
Planning Phase
- System assessment
- Zone mapping
- Infrastructure evaluation
Execution Phase
- Installation timeline
- Testing protocols
- Staff training
Expert Insights, Exceptional Outcomes
Transform challenges into opportunities with Tolj Commercial’s consultation services. Our tailored advice empowers you to make decisions that drive long-term success.
Expert Insights, Exceptional Outcomes
Transform challenges into opportunities with Tolj Commercial’s consultation services. Our tailored advice empowers you to make decisions that drive long-term success.
FAQs
What is temperature zoning in industrial properties?
How does an HVAC zoning system work?
What are the benefits of HVAC zoning in industrial buildings?
Can a zoned HVAC system be integrated into existing ductwork?
What types of buildings benefit most from HVAC zoning?
Conclusion
I’ve seen how proper temperature zoning transforms industrial properties from energy-draining liabilities into efficient, profitable assets. Whether you’re managing a warehouse, pharmaceutical facility, or multi-tenant complex, the right zoning system can dramatically impact your bottom line. Don’t let inefficient temperature control eat into your profits any longer.
Ready to optimize your facility? Schedule a consultation with me. Let’s discuss how we can implement a custom temperature zoning solution that meets your specific needs and drives real results.
Your industrial property’s success is my priority. Let’s make it happen.