Imagine if your building, equipped with the Internet of Things, could tell you exactly when it needed maintenance before anything broke down. Sounds like science fiction, right? Well, folks, welcome to the future – or should I say, the present. Predictive maintenance is revolutionizing how we care for our properties and equipment, and it’s not just a fancy term to impress your colleagues at the water cooler.
In today’s fast-paced industrial world, unexpected breakdowns can cost you more than just a headache – we’re talking serious money down the drain. That’s where predictive maintenance swoops in like a superhero, cape and all, to save the day (and your wallet).
Key Takeaways
- Predictive maintenance can significantly reduce unplanned downtime and extend equipment lifespan
- Implementing predictive maintenance strategies can lead to substantial cost savings and improved operational efficiency
- The future of predictive maintenance lies in advanced AI and machine learning technologies, paving the way for smarter factories
Expert Insights, Exceptional Outcomes
Transform challenges into opportunities with Tolj Commercial’s consultation services. Our tailored advice empowers you to make decisions that drive long-term success.
Understanding Predictive Maintenance
Now, I know what you’re thinking. “Mike, isn’t this just a fancy way of saying ‘fixing stuff before it breaks’?” Well, yes and no. Let’s break it down:
• Reactive maintenance: The “if it ain’t broke, don’t fix it” approach. Spoiler alert: it usually ends up breaking at the worst possible time.
• Preventive maintenance: The “better safe than sorry” method. Regular check-ups, like taking your car for an oil change every 5,000 miles.
• Predictive maintenance: The “crystal ball” of maintenance. Using data analytics and machine learning to predict when maintenance is needed.
Predictive maintenance is like having a fortune teller for your equipment. It uses a cocktail of cool tech – IoT sensors, data analytics, and AI – to monitor your assets in real time. It’s like your equipment is wearing a fitness tracker, constantly checking its vital signs.
The Economics of Predictive Maintenance
Like any good investment, predictive maintenance requires some upfront capital. But trust me, the returns are worth it.
Consider this:
Research by Deloitte suggests that in the age of Industry 4.0, predictive maintenance can deliver impressive results:
- Up to 20% increase in equipment uptime
- Significant reduction in unexpected breakdowns
- Substantial improvement in overall operational efficiency
These figures underscore how predictive maintenance goes beyond just preventing individual asset failures, positioning businesses at the cutting edge of industrial innovation.
Key Areas of Cost Savings
So, where exactly are these savings coming from? Let’s break it down:
- Reduction in unplanned downtime: Surprise breakdowns are like unexpected guests – never welcome and always costly. Predictive maintenance gives you a heads-up, so you can plan around it.
- Extension of equipment lifespan: Treat your equipment right, and it’ll return the favor. Regular, timely maintenance can add years to your assets’ life.
- Optimization of maintenance schedules: No more unnecessary check-ups or last-minute scrambles. It’s like having a personal assistant for your maintenance needs.
- Improved energy efficiency: Well-maintained equipment runs more efficiently. It’s like giving your machinery an energy-boosting smoothie every morning.
- Reduction in spare parts inventory: No more hoarding “just in case” parts. You’ll know exactly what you need and when you need it.
Implementing Predictive Maintenance Strategies
Alright, I’ve convinced you. Predictive maintenance is the bee’s knees. But how do you actually implement it? Here’s a step-by-step guide:
- Assess your current maintenance practices. Are you still using a “break-fix” approach? Time for an upgrade, my friend.
- Identify your critical assets. Not all equipment is created equal. Focus on the big players first.
- Choose your weapons (I mean, technologies). There are a lot of predictive maintenance tools out there. Pick the ones that suit your needs, especially those that integrate well with your existing management system.
- Train your team. Your staff needs to be on board. Think of it as teaching an old dog some very cool new tricks in maintenance management.
- Integrate with existing systems. Predictive maintenance shouldn’t be an island. It needs to play nice with your current setup.
Data-Driven Decision-Making in Predictive Maintenance
Now, let’s talk data. In the world of predictive maintenance, data is king. It’s like the fuel that powers the whole operation. Here’s what you need to know:
• Data quality is crucial. Garbage in, garbage out, as they say. Make sure your data is accurate and relevant.
• Data collection is essential for effective vibration analysis in predictive maintenance. can come from various sources – sensors, maintenance logs, and even equipment manuals. The more, the merrier!
• Predictive analytics can significantly enhance your maintenance management by utilizing big data for better decision-making. is where the magic happens. It’s like having a crystal ball, but instead of a mystical orb, you’ve got algorithms and machine-learning models.
• Real-time data visualization is your window into the soul of your equipment. Dashboards and reports help you see what’s going on at a glance.
The goal here is to make informed decisions that enhance reliability and reduce downtime. With the right data and analysis, you’re not just guessing – you’re making calculated moves like a maintenance chess master.
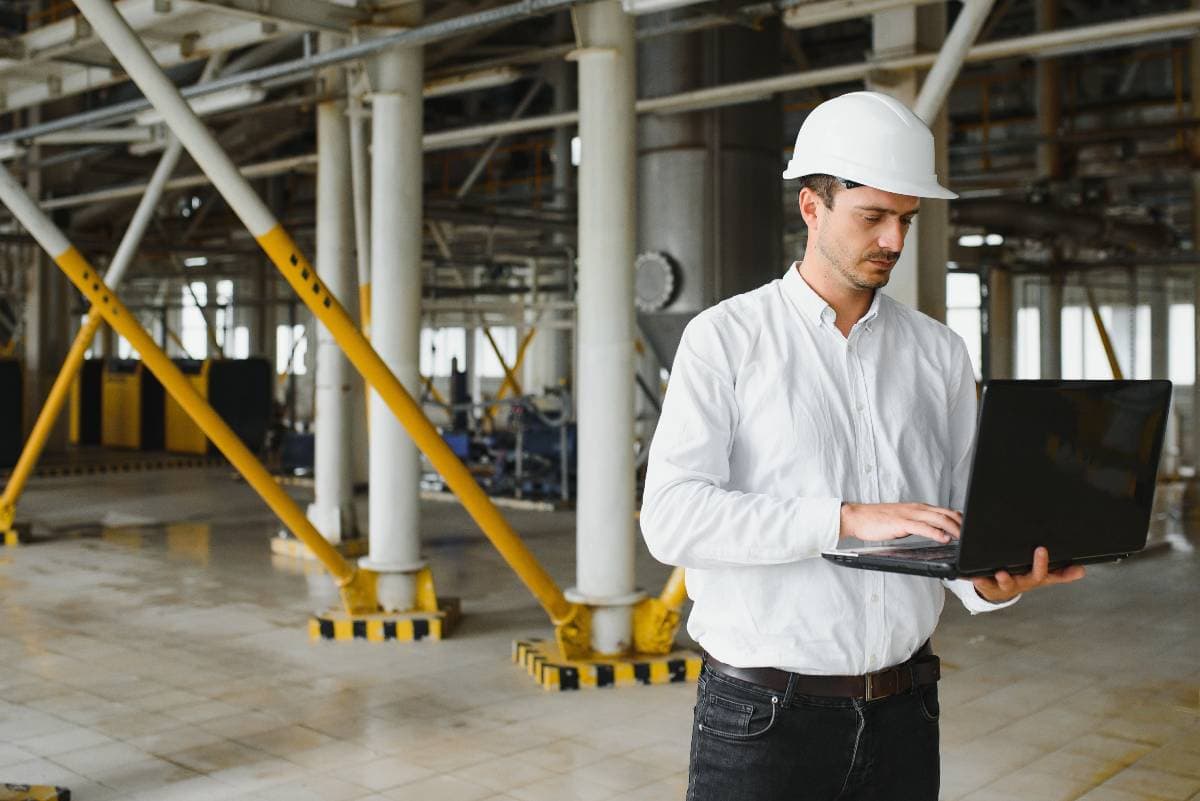
Predictive Maintenance Software and Tools
Now, I’m not going to lie to you – there’s a lot of predictive maintenance software in the maintenance management sector. It’s like being a kid in a candy store, except instead of candy, you’re choosing between different data analysis platforms.
When shopping for predictive maintenance software, keep an eye out for these key features:
First, look for integration capabilities. Your software should play nice with your existing systems, including your CMMS for effective maintenance management. After all, you don’t want to create a digital island in your maintenance department.
Next, prioritize a user-friendly interface. Trust me, you shouldn’t need a PhD in computer science to use this stuff. The best software is intuitive and easy to navigate, even for those of us who still struggle with our smartphone settings.
Scalability is another crucial factor. As your needs grow, your software should be able to keep up. It’s like buying clothes for a growing kid – you want something with room to expand.
Lastly, don’t underestimate the importance of customization options. One size doesn’t fit all in maintenance, and your software should reflect that. You want something that can be tailored to your specific needs and processes.
Some popular options in the market include IBM Maximo, SAP Predictive Maintenance and Service, and Uptake. But remember, the best software for you depends on your specific needs and setup. It’s not about choosing the fanciest or most expensive option – it’s about finding the right fit for your business.
Industry-Specific Applications of Predictive Maintenance
Predictive maintenance isn’t a one-trick pony. It’s making waves across various industries, each with its own unique applications and benefits.
In the manufacturing sector, predictive maintenance keeps production lines running smoothly and reduces costly downtime. Imagine being able to predict when a crucial piece of machinery will need servicing, allowing you to schedule maintenance during planned downtime. It’s like having a crystal ball for your factory floor.
For energy and utilities, predictive maintenance is ensuring the lights stay on and the water keeps flowing. Power plants and water treatment facilities can use this technology to predict equipment failures before they lead to outages or service interruptions. It’s not just about convenience – it’s about maintaining critical infrastructure.
In transportation and logistics, predictive maintenance is keeping vehicles on the road and goods moving. Fleet managers can predict when vehicles will need servicing, optimizing routes and schedules to minimize disruption. It’s like having a psychic mechanic for every truck in your fleet.
The healthcare industry is using predictive maintenance to keep critical medical equipment in top shape. From MRI machines to life support systems, this technology helps ensure that vital equipment is always ready when patients need it most. It’s not just about saving money – it’s about saving lives.
And of course, in commercial real estate – my personal playground – predictive maintenance is a game-changer. Imagine being able to predict when an HVAC system will need servicing, or when a roof might start leaking. It’s like having a sixth sense of your building’s health, allowing you to address issues before they become major problems (and major expenses).
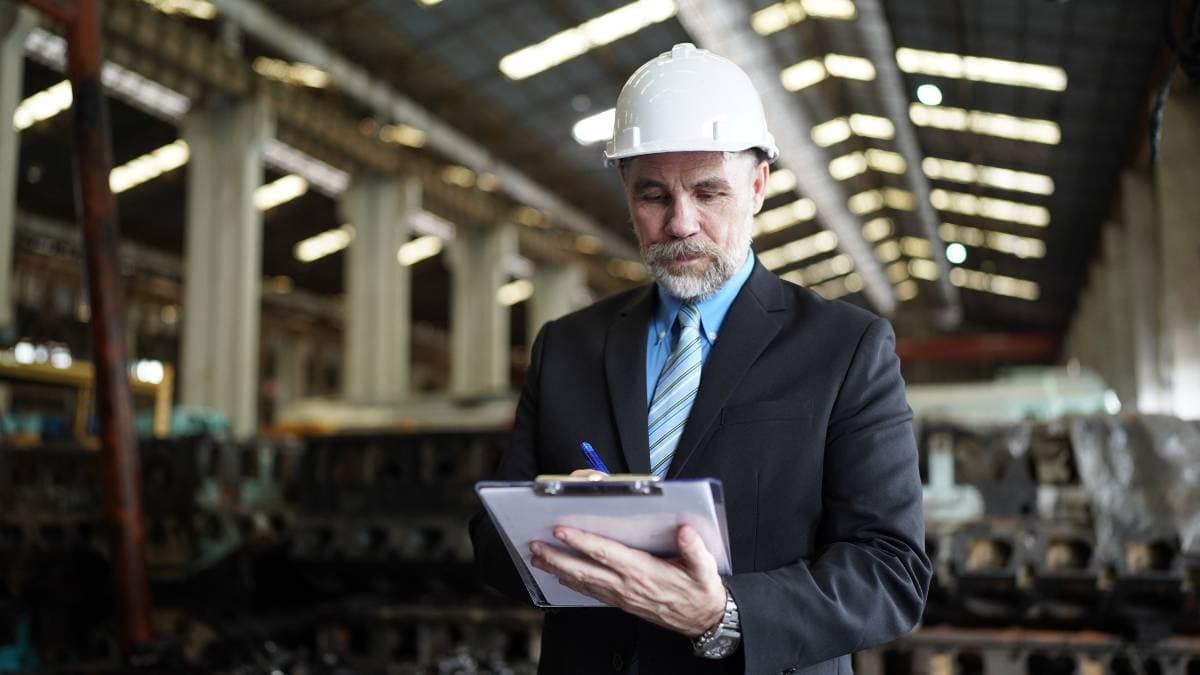
Challenges and Solutions in Predictive Maintenance Adoption
Now, I won’t sugarcoat it – implementing predictive maintenance isn’t all sunshine and rainbows. There are challenges, but don’t worry, they’re not insurmountable.
First up, we have data quality issues. Remember, garbage in, garbage out. Ensuring your data is accurate and complete is crucial. The solution? Implement rigorous data collection and validation processes. It might take some extra effort upfront, but trust me, it’s worth it in the long run.
Next, there’s the skill gap. Predictive maintenance requires a blend of mechanical knowledge and data analysis skills that might not exist in your current team. You might need to upskill your team or bring in new talent to handle the tech side of things. Consider partnering with universities or tech firms to bridge this gap.
Integration with legacy systems can be another headache. Getting new tech to play nice with old systems can be like trying to teach your grandpa to use TikTok. The key here is careful planning and possibly phased implementation. You might also want to consider middleware solutions that can help bridge the gap between old and new.
Finally, there’s often resistance to change. Some folks might be set in their ways. Change can be scary, after all. The solution? Communication and education. Help your team understand the benefits of predictive maintenance. Show them how it can make their jobs easier and more effective. Sometimes, seeing is believing.
Expert Insights, Exceptional Outcomes
Transform challenges into opportunities with Tolj Commercial’s consultation services. Our tailored advice empowers you to make decisions that drive long-term success.
FAQs
How does predictive maintenance differ from preventive maintenance?
What’s the average ROI for implementing predictive maintenance?
Can predictive maintenance be applied to all types of industrial equipment?
How long does it typically take to see cost savings from predictive maintenance?
What role does artificial intelligence play in predictive maintenance?
Conclusion
Let’s wrap this up. Predictive maintenance isn’t just fancy tech talk—it’s your ticket to smoother operations and a healthier bottom line. It’s like having a crystal ball for your equipment, helping you dodge costly surprises.
Ready to step into the future of maintenance? Let’s chat! I’ve been in your shoes, and I’d love to help you navigate this game-changing approach. Schedule a consultation with me, and we’ll explore how predictive maintenance can work for you. Don’t wait for a breakdown—let’s get predictive!