When it comes to warehouse space calculation, you want to make sure that you are making the most of the space that you have. You may be wondering how to do this, and luckily, we have some tips for you! In this blog post, we will discuss some strategies for maximizing your warehouse space. By following these tips, you can improve your productivity and make the most of your workspace.
Warehouse Space Calculation is the process of calculating the amount of space required for storage; It plays a crucial part of any storage project because it helps you to determine how much space you need and how much it will cost.
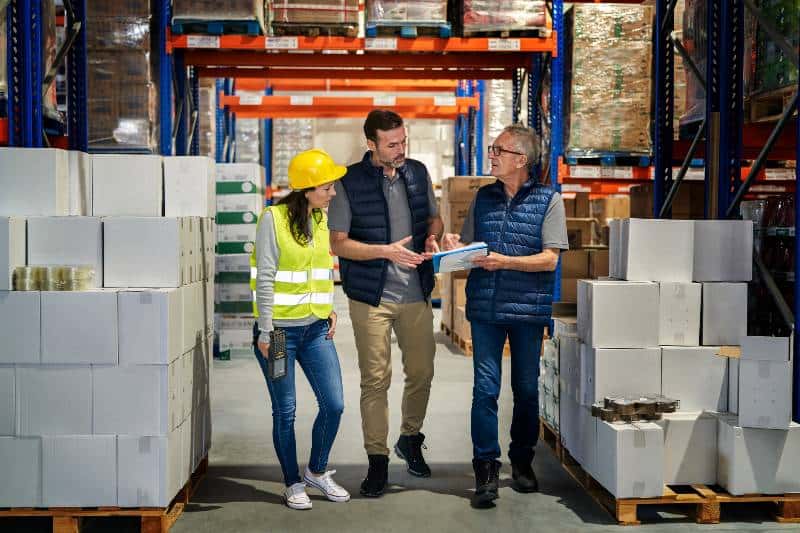
How to do warehouse space calculation and storage capacity
To calculate your warehouse’s storage capacity, you’ll need to know the total square footage of your usable space and your facility’s clear height. Once you have those numbers, simply multiply them to get your total storage capacity in cubic feet.
For example, if your usable space is 80,000 square feet and your clear height is 25 feet, your total storage capacity would be 2,000,000 cubic feet. Keep in mind that this is just an estimate – actual storage capacity may vary depending on the specific layout of your warehouse. Nevertheless, calculating your warehouse’s storage capacity is a helpful first step in determining how much space you have to work with.
Calculating the Total Storage Capacity of Your Warehouse
When it comes to warehouse storage, one of the most important things to consider is the facility’s clear height. This is because the clear height will determine the total storage capacity in cubic feet. To calculate the total storage capacity, simply multiply the total square footage of usable space by the clear height.
For example, if your building has a total square footage of 80,000 and a clear height of 25 feet, its total storage capacity would be 2,000,000 cubic feet. Just keep in mind that this is only an estimate – actual storage capacity may vary depending on factors such as the type of materials being stored and the arrangement of the shelves.
Are You Utilizing All of Your Warehouse Space?
The warehouse is the backbone of your operation. It’s where you store all your inventory and materials, receive shipments from vendors and customers, and ship out orders to customers. Your warehouse is also a critical part of your supply chain, so if it’s not running efficiently, then it can hurt your business.
Learn How to Calculate Warehouse Space Utilization
The first step is understanding how to calculate warehouse space utilization. The standard formula is the number of pallets stored divided by the total number of storage locations. For example, if you have 100 pallets and 500 storage locations, your warehouse space utilization would be 20%.
But there are other factors to consider when calculating warehouse space utilization, such as the type of products being stored and the height of the shelves.
Start Evaluating Your Warehouse Space Utilization
If you want to ensure that your warehouse is running efficiently, then you need to start evaluating your space utilization. By understanding how to calculate it and what factors to consider, you can make sure that you are making the most of your space. Contact us today to learn more about our warehouse optimization services.
How to properly utilize warehouse space
When it comes to warehouse space, there’s a lot to consider. How will you use it? What should you put where? How much space do you need?
The good news is that there are plenty of ways to maximize your warehouse space so that you can get more out of every inch of your company’s warehouse. Here are tips for getting the most out of your warehouse space:
1. Don’t try to fit everything in one room
If you’re working with a small business, odds are that you don’t have big budgets or lots of employees to spare. That means that making smart use of your warehouse space is even more important than usual. Don’t try to fit everything into one room — break up your inventory into multiple rooms based on its purpose or material type. For example, if you sell clothing, keep all your shirts and pants in one place while keeping shoes in another area altogether.
2. Label everything clearly
It’s not enough just to separate items by type; if someone needs something from across the room, they’ll need some way of finding it quickly and easily — labeling each item helps with this process because it makes things easier for anyone who might need to access the item.
Plus, if you ever need to move things around, clear labeling will make it simpler to put everything back in its rightful place.
3. Keep inventory up-to-date
When you’re running a business, it’s extremely important that you have accurate inventory records. That way, if something is missing or damaged, you’ll know about it right away. You can set up an inventory system that accurately tracks everything in your warehouse, so that you never run out of anything important.
4. Use the right container for the right product
One of the tips for getting the most out of your warehouse space is to use the right container for the right product. If you’re storing soft goods like clothes and shoes, you may want to consider using plastic totes with wheels. These lightweight containers are easy to transport and can hold up to 100 pounds of material. They’re also available in a variety of sizes, so they’ll fit any item you want to store.
Some of the most popular storage containers are made from plastic. And it’s no wonder–plastic is lightweight, durable, and easy to clean. Perhaps best of all, plastic containers are stackable, so you can make the most of your storage space. Another key benefit of plastic storage containers is that they sealtightly, keeping out moisture, dust, and pests.
This means your belongings will stay clean and dry, even if you’re storing them in an attic or basement. And if you’re worried about environmental impact, know that many plastic storage containers are now made from recycled materials. So choosing plastic for your storage needs is a smart and responsible choice.
5. Create a system that’s easy on the eyes (and on workers)
This will make it easier for workers to find things as well as get their jobs done more quickly.
The best way to do this is by using color-coded bins and labels. These are inexpensive, easy to implement, and can make a big difference in how much time people spend looking for items in their warehouse.
For example, if you have one bin for each department, then it makes sense to use colors that match the department’s name: red for sales, blue for accounting, purple for shipping, and so on. The same goes for labels — use markers in those same colors so they stand out from other labels.
Increasing current warehouse capacity
If you’re looking for ways to increase the capacity of your warehouse, one option to consider is installing a mezzanine. A mezzanine is an elevated platform that can be used for additional storage or as an office space.
When installed above a floor-level process, like shipping or receiving, it can nearly double your floor space. Mezzanines are a popular choice for warehouses because they’re relatively easy and cost-effective to install. And, because they’re not permanently attached to the building, they can be easily removed or relocated if necessary. If you’re considering adding a mezzanine to your warehouse, be sure to consult with a professional to ensure it meets all safety and code requirements.
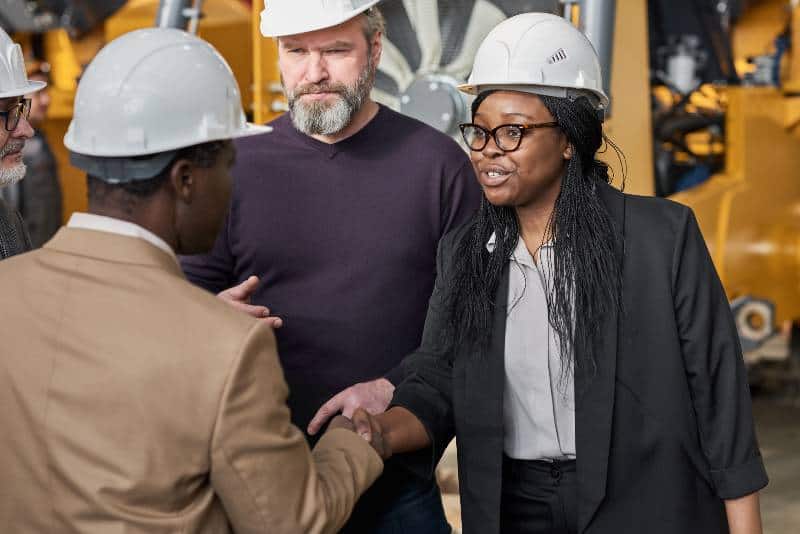
Tips on Maximizing Your Warehouse Storage Capacity
Maximizing your warehouse storage capacity can be a challenge. But with a little planning and some simple changes, you can get the most out of your warehouse space.
Here are some tips for maximizing your storage capacity:
Use the Right Storage Solutions
Maximizing your warehouse storage capacity is using the right usable storage space. If you are looking for a good way to keep all of your products safe and secure, then you should consider investing in a self-storage unit. This will provide you with a lot of benefits, including:
Security
A self-storage unit can help protect your items from theft or other types of damage. They are also kept locked up so that no one else can access them without your permission.
Convenience
With a self-storage unit, there is no need for you to worry about moving things around or finding space for everything. The units can be rented by the month so that you don’t have to worry about paying extra fees if you don’t need the space for an extended period.
Affordability
There are many different sizes of self-storage units available for rent, including small ones that will only hold a few boxes and large ones that can accommodate an entire office building full of furniture! You simply choose the size that works best for your needs and budget!
Rearrange Your Aisles, Pallets, and Racks
The most overlooked way to maximize your warehouse storage capacity is by rearranging your aisle layout. The correct aisle layout will allow you to maximize the amount of space between each rack so that you can fit more pallets on each one. This will also reduce the amount of wasted space in the warehouse since there will be fewer empty spaces between racks where nothing can be stored.
Keep room for expansion
If you know that you will need more space in the future, make sure that you leave room for expansion. This will allow you to easily add on when necessary without having to tear down walls or move equipment around too much. You may even want to consider building an addition to your existing building so that adding new space does not require tearing down walls or moving heavy machinery around too much.
Account for seasonal inventory changes
During the year, there are times when your inventory levels are higher than others. For example, during the holidays you may have more items in stock than at other times of the year. If you have a warehouse storage capacity problem, this can be especially problematic during these times of high demand.
To help manage this issue, account for seasonal inventory changes and plan your space accordingly. You may need to rent additional space or purchase more shelving units to accommodate your inventory needs at certain times of the year.
If you don’t account for these seasonal changes, you could end up with excess inventory that is taking up valuable warehouse storage space that could be used for other purposes. In addition to paying rent on this extra space, you’re also paying for insurance, utilities, and maintenance costs that may not be necessary if you were using just enough space for your business needs during those times of high demand.
Increase your vertical height
Maximizing your warehouse storage capacity is not easy. Many factors can limit how much you can store in your warehouse, including the buildings’ physical limitations and the nature of the product itself.
One way to maximize storage capacity is to increase your vertical height. For example, if you have a warehouse that’s 30 feet tall and you’re storing products on shelves that are 10 feet off the ground, you only have 20 feet of space for storage. If you raised those shelves to 20 feet off the floor, you would have 40 feet of space for storage.
This is an easy solution for maximizing storage capacity — but it’s not always possible because it may require changing certain aspects of your facility. For example, if you’re using mezzanines as part of your industrial shelving system, then raising them might require adding support beams or columns to ensure that they don’t collapse under their own weight or stress from other equipment in the area (such as forklifts).
Avoid Estimating Warehouse Storage Capacities
Here are some reasons why:
Estimating Warehouse Storage Capacity is Difficult
You are likely to underestimate the amount of space you need for your inventory. This is especially true if you have never done this before. If you underestimate the space required for your inventory, then you will not be able to store it properly and it will take up too much space in your warehouse. This will reduce your profits and increase the risk of damage to your inventory.
It Can Be Costly to Adjust Your Warehouse Layout Afterward
If you overestimate or underestimate the amount of space required by your inventory, then it may be costly to adjust your warehouse layout afterward. For example, if you overestimate the space because you have never done this before, then it may cost thousands or even millions of dollars to reconfigure the layout once again after realizing that there is not enough room for everything.
On the other hand, if you underestimate the amount of space needed by underestimating warehouse storage capacities, then it may cost thousands or even millions of dollars to reconfigure the layout once again after realizing that there is too much space and not enough inventory to fill it.
You May Not Be Able to Accommodate Future Growth
If you underestimate the amount of warehouse storage space you need, then you may not be able to accommodate future growth. This could lead to lost sales and profits, as well as the need to reconfigure your warehouse layout again at a later date.
It’s important to take the time to accurately estimate the amount of space you need for your inventory. This will help you avoid many of the problems listed above and ensure that you have enough space for everything.
Conclusion
So, what’s the best way to go about calculating warehouse space needs? The first step is understanding your inventory turnover rate. This will help you determine how much storage space you need on a monthly basis. Once you know how much space you need each month, use our warehouse size calculator to get an idea of what kind of facility will work best for your business.
And finally, don’t forget to factor in extra space for future growth! If you have any questions or want more information on calculating your warehouse space needs, give us a call or schedule a free consultation. I would be happy to help!